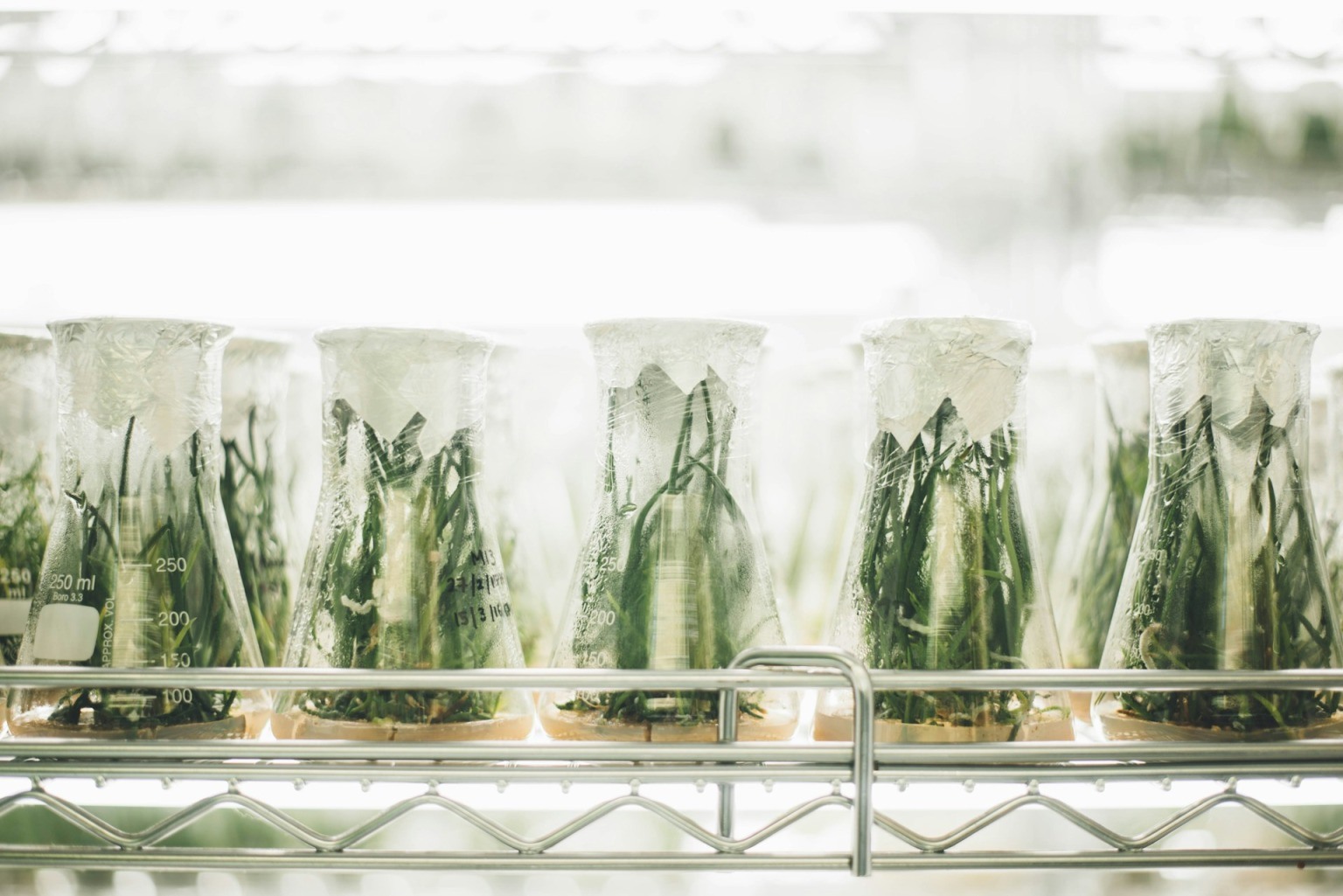
How to use greenhouse gases to our advantage
Kelly Kousi
As global demand for clean and sustainable energy accelerates, the offshore wind sector faces a growing dilemma: what happens to massive steel jackets, towering pylons and composite blades once they retire? Without intentional planning, these materials can clog landfills, squander embedded energy and generate new environmental burdens. Embracing offshore circular-economy principles promises to transform tomorrow’s “waste” into today’s resource.
Imagine jacket foundations engineered with bolted flanges instead of permanent welds. At the end-of-life, entire jackets can be lifted intact, avoiding cutting and grinding. In a North Sea pilot, two decommissioned jackets were refitted as artificial reefs: steel modules now support mussel beds and kelp forests, boosting local biodiversity while cutting new steel emissions by 30 percent. These same jackets will later serve as substructures for next-generation turbines, slashing foundation costs and delivering carbon savings in the hundreds of tons per unit. Industry consortia and turbine manufacturers are now launching “take-back programs” and digital exchanges for reclaimed structures and fibers, ensuring that decommissioned jackets, blades, and alloys flow back into new projects and drive down lifecycle costs.
Similarly, thermoplastic composite blades are on the verge of commercial reality. Conventional epoxy-based blades resist breakdown, forcing energy-intensive post-treatment that yields low-value products outside of market standards for reuse. New blade designs replace epoxies with reversible polymers that soften in warm water baths, releasing continuous glass or carbon fibers. Danish trials have shown that reclaimed fibers, with over 90 percent of their original tensile strength, can reinforce marine-grade concrete used for offshore platforms, walkways, and scour protection. By replacing up to 40 percent of virgin aggregate, these concretes meet or exceed industry durability standards, all while reducing CO₂ in cement production.
Policy frameworks are aligning similarly accelerating these innovations. Under the European Green Deal’s Circular Economy Action Plan, EU member states must recycle or reuse at least 80 percent of offshore-wind materials by 2035. Feed-in tariffs now include a “circularity premium,” rewarding projects that achieve certified design-for-disassembly. Horizon Europe grants cover up to 60 percent of R&D costs for modular jacket systems and reversible-resin blades. In the UK, the Crown Estate is piloting material-passport requirements: each component ships with a digital record of its chemistry, manufacturing data, and disassembly instructions, ensuring traceability and simplifying end-of-life planning.
At the same time, the economic benefits also enhance the environmental value. Reusing jackets saves millions on steel procurement and fabrication, while reclaimed fibers fetch premium prices in specialty cement markets. Operators report disposal fee reductions of up to 70 percent when components enter certified recycling channels. Secondary markets for reclaimed alloys and composites are emerging in Europe and Asia, offering predictable revenue streams that improve project bankability.
Beyond material flows, circular offshore wind farms can foster symbiosis with the marine environment. Artificial-reef jackets enhance local fisheries and support research into ecosystem resilience. Concrete modules reinforced with thermoplastic fibers provide stable substrates for sea-grass restoration. Even cables can be recovered and repurposed: copper and aluminum alloys are reannealed for subsea electrification elsewhere, closing the loop on undersea infrastructure.
Achieving a truly circular offshore wind industry requires collaboration across engineering, policy, and marine science. Manufacturers should standardize quick-release connections and adopt reversible polymers. Developers and leaseholders need contractual incentives to return used components. Regulators should harmonize material-passport standards internationally, preventing fragmentation of recycling streams. Industry consortia and turbine manufacturers are now launching “take-back” programs and digital exchanges for reclaimed structures and fibers, ensuring that decommissioned jackets, blades, and alloys flow back into new projects and drive down lifecycle costs.
The prize is immense: an offshore wind sector where every bolt, blade, and beam is part of a continuous resource cycle—powering today’s grids and laying the groundwork for tomorrow’s installations. By designing targeted disassembly, championing reuse pilots, and embedding circularity into policy, we can ensure that offshore wind remains a model of sustainability, long after the current energy market trend has passed.
Sources:
TWI-global
EU Circular economy action plan
INSITE Phase 2 Report, Understanding the INfluence of man-made Structures In The marine Environment
Marine Data Exchange
Written evidence submitted by The Crown Estate
Kelly Kousi
Anastasia Papangelou
Aglaia (Lina) Ntokou
Viktoria Taroudaki